Geringere Kosten bei verbesserter Qualität
Produktionsbereich allgemein
STW gehört zu den europäischen Herstellern moderner Technik für die Getränkeindustrie. Speziell mit Komponenten rund um Edelstahlverrohrungen ist der Mittelständler führend. Tausende Schweißnähte pro Ventilknoten werden wirtschaftlich wie zuverlässig realisiert. Dabei kommt eine neue, Industrie-4.0-taugliche Stromquelle von Orbitalum zum Einsatz.
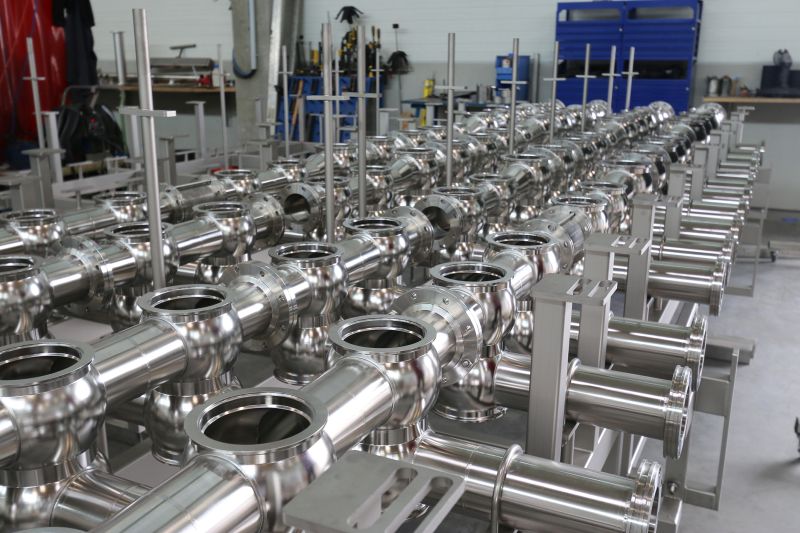
Hochwertige Ventilknoten von STW sind wichtige Bauteile in Produktionsanlagen der Lebensmittel- und Getränkeindustrie. Bild: Walter Lutz
In der Lebensmittel- und Getränkeindustrie geht es bei der Prozesstechnologie nicht nur um die Zuverlässigkeit und Wirtschaftlichkeit der Anlagen, sondern auch um die Einhaltung hoher Hygienestandards. Eine Vielzahl von Ventilen sorgt bei flüssigen Medien für deren richtigen Zu- und Abfluss. Dabei dominieren heute zunehmend sogenannte Ventilknoten, die beim Hersteller schon zu kompletten Einheiten individuell aus Passstücken, Rohren und Ventilen aufgebaut werden. »Genau hierauf haben wir uns spezialisiert und beliefern Anlagenbauer in der ganzen Welt«, erklärt STW-Geschäftsführer Georg Slavik. Seit dem Gründungsjahr 2000 hat sich der zertifizierte Schweißfachbetrieb fokussiert auf die besonderen Anforderungen im Edelstahl-Rohrleitungsbau nach AD 2000-Merkblatt HP 0 / HP 100 R / DIN EN ISO 3834-2. Gut 150 dieser komplexen Baugruppen bauen die rund 60 Mitarbeiter jährlich.
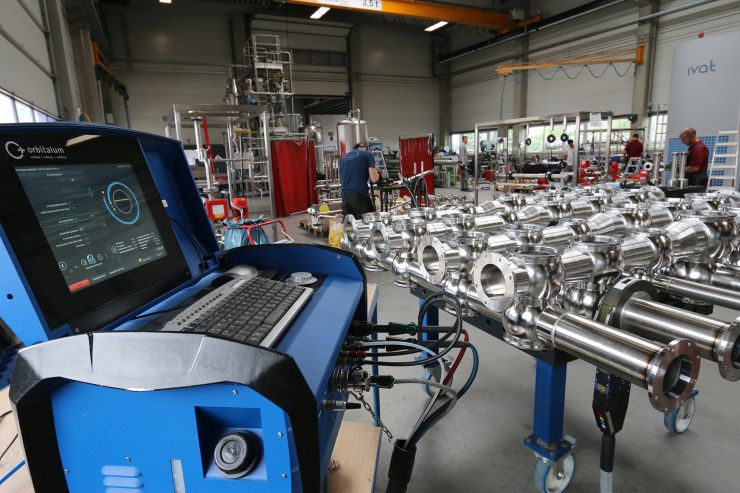
Die Stromquelle »Orbimat 180 SW« überzeugt mit leichter Bedienbarkeit per Touchscreen oder Drehsteller. Bild: Walter Lutz
Wurden früher die Edelstahlrohre mit den Ventilgehäusen und Flanschen per Hand verschweißt, kommt bei STW seit einigen Jahren die Orbitalschweißtechnik des Singener Herstellers Orbitalum zum Einsatz. Fertigungsleiter Andree Müller erläutert dazu: »Mit dieser Technik erreichen wir eine gleichbleibend gute Qualität der Schweißnähte, weil sie keine Probleme mit Ermüdung oder Konzentration hat. Wir entlasten unsere Schweißer von der Routine, sodass sie sich ganz auf die Fertigungsüberwachung konzentrieren können.« Seit Kurzem setzt das Unternehmen auch die neue Stromquelle »Orbimat 180 SW« des Singener Unternehmens ein. »Sie ist Industrie-4.0-tauglich, weil erstmals eine digitale Vernetzung von Mensch und Maschine mit einer umfassenden Dokumentation möglich ist«, ergänzt Müller. Die Schweißstromquelle verbindet den orbitalen Schweißprozess mit moderner Informations- und Kommunikationstechnik und sorgt für bestmögliche Schweißergebnisse, hohe Wirtschaftlichkeit, nachhaltiges Qualitätsmanagement und eine hohe Prozesssicherheit. Die lückenlose Datenaufzeichnung und -sicherung im LAN des Anwenders bringen eine hohe Transparenz, wie sie Industrie 4.0 fordert. Alle Daten können im internen Systemspeicher und auf einem externen USB-Datenträger gesichert werden. Neben den schweißtechnisch relevanten Basisparametern, zum Beispiel verwendetes Gas, Rohrdurchmesser, Material und Wandstärke, kann der Kunde weitere Daten festlegen, beispielsweise den Bediener, den Gaslieferanten oder den Bauteilhersteller. Erst wenn die gewünschten Informationen vorliegen, startet die Stromquelle den Schweißprozess.
Bessere Planung
Über die integrierte LAN- und WLAN-Schnittstelle lässt sich das Gerät ins Netzwerk einbinden: Der gesamte Schweißprozess kann so unmittelbar nachverfolgt werden, weil Bediener, Arbeitsvorbereiter und Qualitätssicherer über unterschiedliche Benutzerebenen jederzeit Zugriff auf Projekte und Daten haben. Alle Schweißdaten und -programme jeder einzelnen Schweißung sind lückenlos abruf- und dokumentierbar, können analysiert und für künftige Schweißungen übernommen oder optimiert werden. Produktionsabläufe lassen sich so besser planen, sind außerdem sicherer sowie kosten- und zeitsparender. Durch den zentralen Datenpool ist es möglich, auf alle Variablen der Stromquellen im Netzwerk zuzugreifen. Sie sind so wichtige Bausteine beim Aufbau eines nachhaltigeren Qualitätsmanagements. Vier USB-Anschlüsse eröffnen zudem weitere Konnektivität.
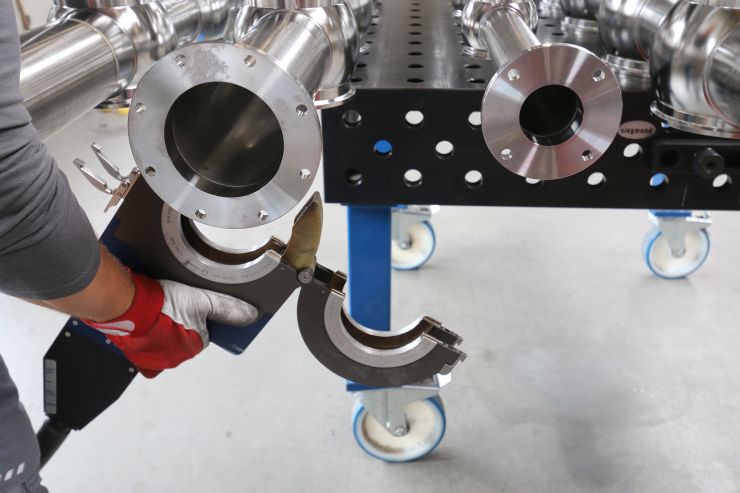
Saubere Arbeit: Der Schweißkopf wird am Edelstahlrohr positioniert. Dank der geschlossenen Schweißkammer dringen Gas und Lichtbogen nicht nach außen. Bild: Walter Lutz
»Unsere Mitarbeiter schwören mittlerweile auf die leichte wie sichere Bedienbarkeit des Systems«, sagt STW-Fertigungsleiter Müller. Bedient wird das Gerät über das große 12,4-Zoll-Farb-Touchdisplay oder alternativ mit dem multifunktionalen Drehsteller. Die grafikunterstützte, mehrsprachige Menüoberfläche ermöglicht eine einfache und intuitive Bedienung und Parametrierung der Schweißstromquelle. Über Softkeys sind wichtige Befehle direkt aufrufbar. Das Betriebssystem läuft selbst nach abrupten Systemabschaltungen und Stromausfällen, wie sie zum Beispiel auf Baustellen vorkommen, ohne Datenverlust wieder an. »Das bringt uns in der Fertigung die höchstmögliche Sicherheit«, so Müller. »Durch die integrierte Auto-Programmierfunktion mit vielen hinterlegten Schweißprogrammen haben wir in der Regel einen Optimierungsbedarf von unter 10 Prozent. Durch wenige Probeschweißungen kommen wir schnell zum bestmöglichen Schweißergebnis.«
Geringere Kosten
Der »Orbimat 180 SW« steigert die Effizienz in Prozessen auch aufgrund der digitalen und präzisen Schweißgasregelung. Diese ermöglicht Schweißungen mit höchstmöglicher Reinheit bei geringem Gasbedarf, was die Kosten pro Schweißung senkt. Die im Schweißprogramm gespeicherten Gasmengenwerte führen so zu reproduzierbar guten Schweißergebnissen. Mit der automatischen Rotor-Stopp-Funktion ergibt sich eine höhere Sicherheit: Wird der Schweißkopfrotor im automatischen Umlauf durch Schwergängigkeit oder durch ein Hindernis am Rotationsvorgang gehindert, stoppt die Stromquelle dank Drehmomentkontrolle unmittelbar die Rotorbewegung des Schweißkopfs. Daraus ergeben sich eine signifikant höhere Lebensdauer des Schweißkopfs sowie deutlich niedrigere Servicekosten. Teure Produktionsausfälle durch Ausschuss werden vermieden.
Um die Gasvor- und -nachströmzeiten zu minimieren, hat Orbitalum eine Flow-Force-Funktion integriert, die den Schweißprozess bei Verwendung von geschlossenen Schweißköpfen entscheidend verkürzt: Durch die digitale Gassteuerung wird Schutzgas mit sehr hohem Volumenstrom direkt vom Druckminderer in den Schweißkopf geleitet. Der unerwünschte Restsauerstoff wird dabei stoßartig ausgespült. Die dadurch reduzierten Vor- und Nachströmzeiten ergeben kürzere Prozesszeiten, verbrauchen weniger Schutzgas und erhöhen somit die Produktivität. Außerdem ergibt sich eine längere Standzeit der Schweißelektrode. Denn durch die optional einstellbare Permanent-Gas-Funktion wird das Eindringen von Sauerstoff in den Schweißkopf auch während der Nebenzeiten verhindert. Dadurch erreicht das System nahezu anlauffreie Nähte bei gleichzeitig niedrigen Prozesszeiten.
»Wir verwenden für die unterschiedlichen Rohrdurchmesser vier verschiedene ›Orbiweld‹-Schweißköpfe, mit denen wir Durchmesser von 3 bis 170 Millimeter bearbeiten können«, so Müller. Die Stromquelle erkennt automatisch den jeweils angeschlossenen Kopf, sodass der Bediener vor Schweißbeginn lediglich sein vorgegebenes Schweißprogramm aufrufen und den Prozess starten muss.
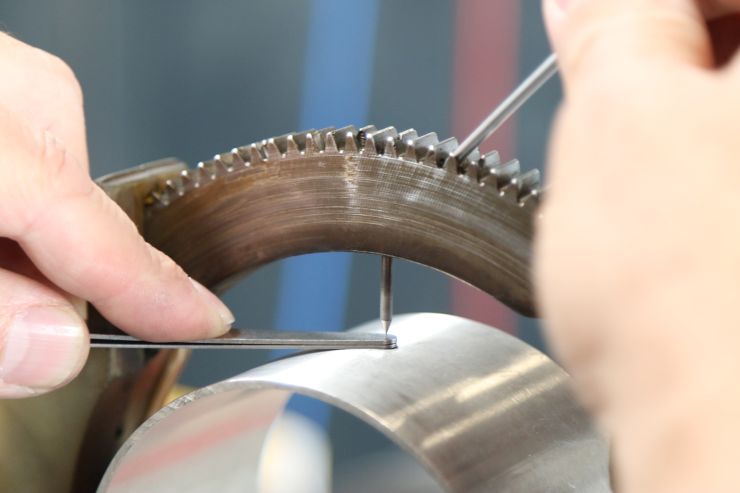
Bei geöffnetem Schweißkopf gelingt die exakte Einstellung der Schweißelektrode zum Rohr hin im Handumdrehen. Bild: Walter Lutz
Gutes Handling
Die Stromquelle verfügt über ein formschönes, praktisches Gehäuse mit seitlich integrierten Tragegriffen. Anschlüsse an der Gerätefront und Rückseite liegen zurückgesetzt geschützt vor mechanischen Beschädigungen. Der klappbare Deckel mit seinem großen Farbdisplay schützt im geschlossenen Zustand die Bedienelemente, den Systemdrucker und den Drehsteller.
Vor etwa 20 Jahren, als Orbitalum in die Orbitalschweißtechnologie einstieg, wurden im Rohrbereich noch über 70 Prozent von Hand geschweißt, heute sind es weniger als fünf Prozent Handarbeit. Das bestätigt auch Andree Müller: »Nur noch die wenigen individuellen Schweißstellen machen wir noch von Hand. Demgegenüber stehen über 100.000 Orbitalnähte im Jahr.«