Orbitalschweißen: Hygienequalität und saubere Verbindungen
Produktionsbereich allgemein
In der Lebensmittel- und Getränkeindustrie geht es bei der Prozesstechnologie nicht nur um Zuverlässigkeit und Wirtschaftlichkeit der CIP-tauglichen Anlagen, sondern zwingend auch um die Einhaltung hoher Hygienestandards. Das Orbitalschweißen bringt hohe Verfahrenssicherheit und Reproduktionsfähigkeit, eine gleichbleibend gute Qualität der Schweißnaht sowie die einfache Bedienbarkeit des Prozesses.
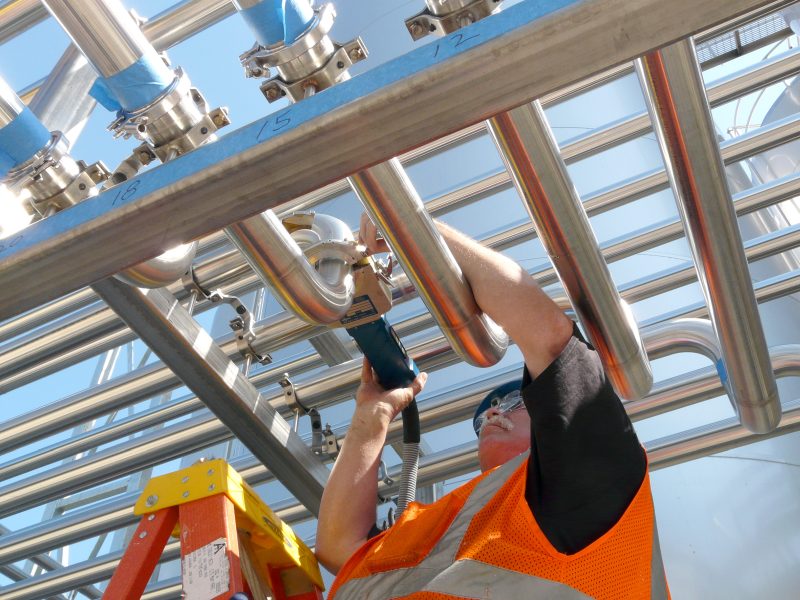
Im Laufe der Entwicklung sind Orbitalschweißköpfe immer kompakter geworden und ermöglichen daher sichere Schweißungen auch unter beengten Platzverhältnissen. Bilder: Orbitalum
In Branchen, die das Verschweißen von Edelstahlrohren in gleichbleibend guter Qualität erfordern, kann das Orbitalschweißen seine Vorteile ausspielen – beispielsweise in der Lebensmittelindustrie, wenn es um glatte Innenflächen von Rohren in CIP-Anlagen geht. Bei Getränkeproduktion in Brauereien und Abfüllanlagen sorgen zum Beispiel eine Vielzahl von Ventilen für die richtigen Zu- und Abflüsse durch die Rohre. Dabei kommen zunehmend sogenannte Ventilknoten zum Einsatz, aufgebaut aus Passstücken, Rohren und Ventilen, die sicher und hygienisch einwandfrei verschweißt werden müssen. Aufgrund strengerer Anforderungen, gesteigertem Qualitätsbewusstsein sowie Facharbeitermangel setzen Hersteller dieser Produktionsanlagen immer mehr auf Orbitalschweißsysteme. Auch die zunehmende Dokumentationspflicht tut ihr Übriges, denn dank intelligenter Schweißstromquellen und definierter Prozesse entspricht dieses Verfahren den internationalen Anforderungen.
Orbitalschweißkopftypen für dünnwandige Rohre
Bei dünnwandigen Rohren bis etwa 170 Millimeter Durchmesser und Wandstärken von 0,3 bis circa 3,5 Millimeter kommen geschlossene Köpfe und das Wolfram-Inertgas-Schweißverfahren (WIG) zum Einsatz. Der Schweißprozess läuft dabei unter gleichbleibenden Bedingungen im Orbitalschweißkopf ab, der das Rohr komplett umgibt. Unter permanenter Schutzgasatmosphäre wird eine WIG-Elektrode über den Schweißkopfrotor definiert um das Rohr herumgeführt. Die zu verschweißenden Rohre werden stumpf (spalt- und versatzfrei) durch einen Lichtbogen miteinander verschweißt. Das setzt eine gute Nahtvorbereitung voraus: rechtwinklig getrennte Rohre, eine gleichbleibend plane Anfasung sowie eine metallisch saubere und gratfreie Oberfläche können durch Einsatz moderner Orbitalrohrtrenn- und -anfasmaschinen erzielt werden.
Die Abmessungen der geschlossenen Schweißköpfe wurden im Laufe der Entwicklung immer kompakter, sodass heute auch unter beengten Montageverhältnissen geschweißt werden kann. Das Handling des Schweißverfahrens am Beispiel der geschlossenen Schweißköpfe ist einfach: Der Kopf wird aufgeklappt und die beiden zu verschweißenden Rohre spaltfrei eingelegt. Der Rohrstoß wird zur Elektrode hin ausgerichtet. Nach Verschließen des Kopfes wird mit dem Startvorgang der flüssigkeitsgekühlte Kopf mit Argongas zuverlässig geflutet. Nach der Lichtbogenzündung fährt die Elektrode sauber um das Werkstück herum.
Anlauffarben werden durch die permanente Schutzgasabdeckung vermieden. Die Schweißung läuft automatisch, versatz- und spaltfrei in gleichbleibend hoher Qualität ab. Die entstehenden sauberen Schweißnähte sorgen im Betrieb für eine hygienegerechte Schweißung und gute Reinigungsmöglichkeiten, da sich Verunreinigungen gut wegspülen lassen.
Stromquelle mit Zugriff auf
Projekte und Parameter
Das Orbitalschweißen punktet außerdem mit intelligenten Schweißstromquellen. Geräte wie der »Orbimat 180 SW« von Orbitalum Tools verbinden dazu den orbitalen Schweißprozess mit moderner Informations- und Kommunikationstechnik und sorgen für gleichbleibend hervorragende Schweißergebnisse, hohe Wirtschaftlichkeit, nachhaltiges Qualitätsmanagement und eine besonders hohe Prozesssicherheit. Die lückenlose Datenaufzeichnung und -sicherung im LAN des Anwenders bringen eine hohe Transparenz, wie sie Industrie 4.0 fordert. Über das MQTT-Protokoll erfolgt die Datenübertragung. Alle Daten werden zudem im internen Systemspeicher und auf einem externen USB-Datenträger gesichert. Neben Daten wie Rohrdurchmesser, Materialqualität und Wandstärke können Anwender weitere Parameter festlegen, zum Beispiel Bedienperson, verwendetes Gas, Gaslieferant, Bauteilhersteller und noch mehr. Erst wenn die gewünschten Informationen vorliegen, startet der »Orbimat 180 SW« den Schweißprozess.
Über die integrierte LAN- bzw. WLAN-Schnittstelle lässt sich das Gerät ins Kundennetzwerk einbinden: Der gesamte Schweißprozess kann so unmittelbar nachverfolgt werden, weil Bedienpersonal, Arbeitsvorbereitung und Qualitätssicherung über unterschiedliche Benutzerebenen jederzeit Zugriff auf Projekte und Daten haben. Alle Schweißdaten und -programme jeder einzelnen Schweißung sind lückenlos abruf- und dokumentierbar, können analysiert und für künftige Schweißungen übernommen oder optimiert werden. Produktionsabläufe lassen sich so besser planen, sind außerdem sicherer sowie kosten- und zeitsparender. Der »Orbimat 180 SW« ist damit ein wichtiger Baustein beim Aufbau eines nachhaltigeren Qualitätsmanagements.
Bessere Bedienung mit intuitiver Menüoberfläche
Passend zur modernen Fertigungsumgebung in der Lebensmitteltechnik ist die Schweißstromquelle in einem formschönen wie praktischen Gehäuse mit seitlich integrierten Tragegriffen untergebracht. Anschlüsse an der Gerätefront und -rückseite liegen zurückgesetzt geschützt vor mechanischen Beschädigungen.
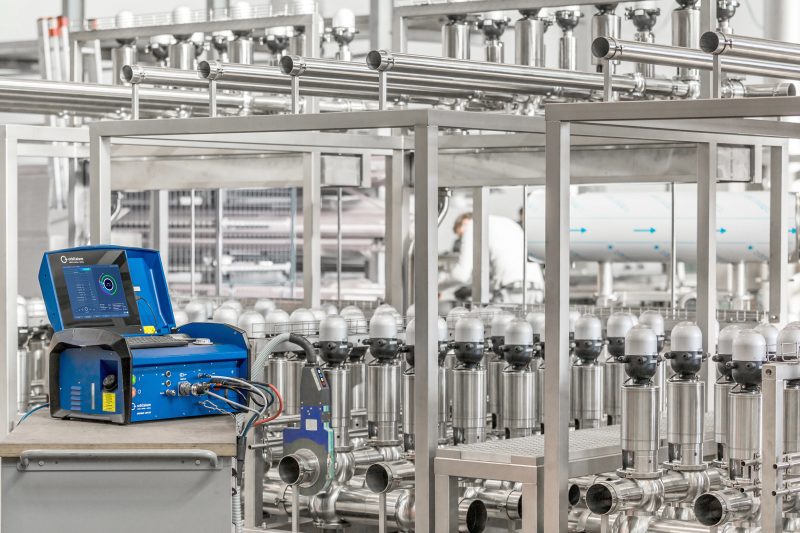
Die Schweißstromquelle bietet leichte Bedienbarkeit per Touchscreen oder Drehsteller.
Der klappbare Deckel mit seinem großen Farbdisplay schützt im geschlossenen Zustand die Bedienelemente, den Systemdrucker und den Drehsteller.
Bedient wird das Gerät über das große 12,4-Zoll-Farb-Touch-Display oder alternativ mit dem multifunktionalen Drehsteller. Die grafikunterstützte, mehrsprachige Menüoberfläche ermöglicht eine einfache sowie intuitive Bedienung und Parametrierung der Schweißstromquelle. Über Softkeys sind wichtige Befehle direkt aufrufbar. Das Gerät arbeitet mit einem Betriebssystem, das selbst nach abrupten Systemabschaltungen und Stromausfällen ohne Datenverlust sauber wieder anläuft.
Die Schweißstromquelle bietet auch aufgrund der digitalen und präzisen Schweißgasregelung eine höhere Effizienz der Prozesse. Die digitale Regelung ermöglicht Schweißungen mit höchstmöglicher Reinheit bei geringem Gasbedarf, was die Kosten pro Schweißung senkt. Die im Schweißprogramm gespeicherten Gasmengenwerte führen so zu reproduzierbar guten Schweißergebnissen.
Mit der automatischen Rotor-Stopp-Funktion ergibt sich eine höhere Sicherheit: Wird der Schweißkopfrotor im automatischen Umlauf durch Schwergängigkeit oder durch ein Hindernis am Rotationsvorgang gehindert, stoppt die Stromquelle dank Drehmomentkontrolle unmittelbar die Rotorbewegung des Schweißkopfes. Mensch und Maschine werden dadurch besser geschützt, teure Produktionsausfälle durch Ausschuss vermieden und Servicekosten gesenkt. Gleichzeitig erhöht sich die Lebensdauer des Schweißkopfes.
Kürzere Schweißzyklen und
höhere Produktivität
Um die Gasvor- und -nachströmzeiten zu minimieren, hat Hersteller Orbitalum seine »Flow-Force«-Funktion integriert, die den Schweißprozess bei Verwendung von geschlossenen Schweißköpfen entscheidend verkürzt: Durch die digitale Gassteuerung wird Schutzgas mit sehr hohem Volumenstrom direkt vom Druckminderer in den Schweißkopf geleitet und der unerwünschte Restsauerstoff wird dabei stoßartig ausgespült.
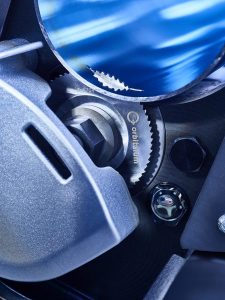
Mit Rohrtrenn- und Anfassmaschinen gelingt die bestmögliche Nahtvorbereitung für das Orbitalschweißen.
Die so reduzierten Vor- und Nachströmzeiten ergeben deutlich kürzere Prozesszeiten, verbrauchen weniger Schutzgas und erhöhen somit die Produktivität. Zudem ergibt sich eine längere Standzeit der Schweißelektrode, denn durch die optional einstellbare Permanentgasfunktion wird das Eindringen von Sauerstoff in den Schweißkopf auch während den Nebenzeiten verhindert. Dadurch erreicht das System nahezu anlauffreie Nähte bei gleichzeitig niedrigen Prozesszeiten.
Wie bei allen »Orbimat«-Stromquellen erkennt auch der »180 SW« automatisch den jeweils angeschlossenen Kopf, sodass der Bediener vor Schweißbeginn lediglich sein vorgegebenes Schweißprogramm aufrufen und den Prozess starten muss.